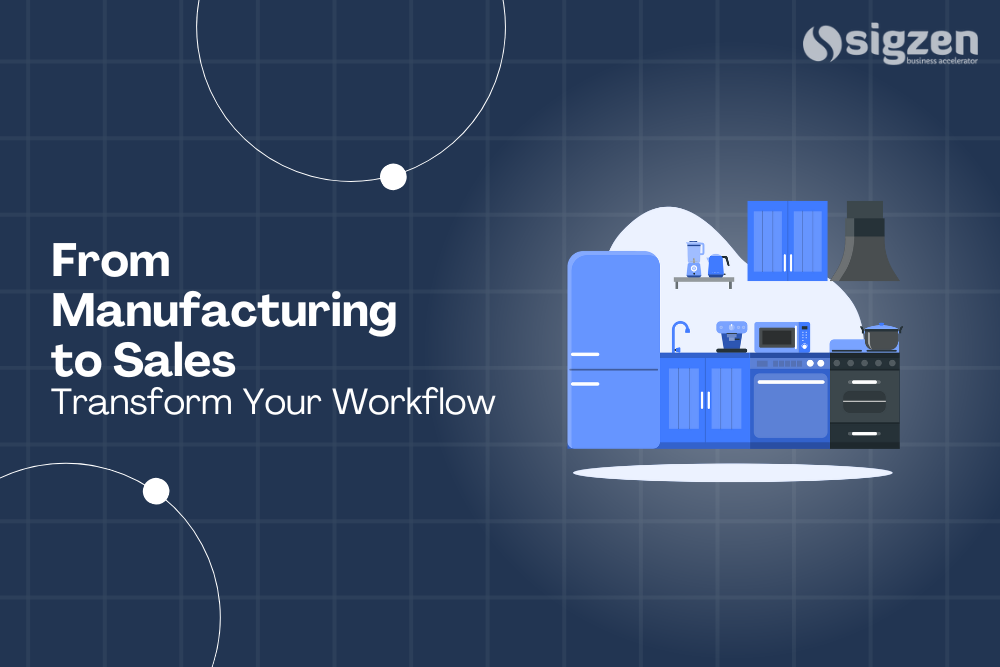
Introduction: The Importance of Quality Management in the Ceramic and Faucets Industry
In the ceramic and faucets industry, the quality of products is paramount. Whether you’re manufacturing ceramic tiles, bathroom fixtures, or faucets, ensuring that every product meets the highest standards is essential for maintaining brand reputation and customer trust. However, managing quality manually or with traditional methods can lead to inefficiencies, inconsistencies, and costly errors.
This is where ERP for Ceramic and Faucet Industry comes in. With ERPNext’s powerful quality management module, ceramic and faucet manufacturers can streamline their quality control processes, reduce defects, and enhance overall product quality. By integrating quality control with other aspects of the business—such as inventory management, procurement, and production—ERPNext ensures that your quality standards are consistently met while optimizing efficiency.
In this article, we’ll explore how ERPNext can help ceramic and faucet businesses improve their quality management processes, reduce wastage, and ultimately deliver high-quality products to the market.
How ERPNext Enhances Quality Management for Ceramic and Faucet Businesses
Quality management is critical in manufacturing industries like ceramics and faucets, where defects can lead to costly recalls and damage to brand reputation. By integrating quality control directly into the ERP system, businesses can improve traceability, streamline inspections, and ensure compliance with industry standards.
1. Streamlined Quality Control with ERPNext
ERPNext offers an integrated ERP quality management module that helps ceramic and faucet manufacturers perform thorough quality checks at every stage of production. Key features include:
- Automated Quality Inspections: With ERPNext, businesses can automate quality inspections during production, reducing the chances of defects being overlooked.
- Real-Time Data: Track real-time data on quality metrics, such as product specifications and inspection results, directly within the ERP system. This enables timely identification of issues and corrective actions.
- Inspection Reports: ERPNext generates detailed inspection reports, helping businesses document compliance with quality standards and industry regulations.
2. Tracking and Tracing Products with Ease
For businesses in the ceramic and faucet industry, traceability is crucial to ensure that quality standards are maintained at all times. ERPNext provides the ability to:
- Track Raw Materials: Track the quality of incoming raw materials, such as clay, metals, or ceramics, before they are used in the production process.
- Product Traceability: From production to finished goods, ERPNext enables manufacturers to trace the quality of individual products, ensuring full accountability.
- Batch Tracking: ERPNext allows businesses to track quality across batches, reducing waste and ensuring that only products meeting quality standards reach the customer.
By providing transparency and traceability, ERP systems for manufacturing companies can reduce the risk of quality issues and improve overall production processes.
3. Seamless Integration of Quality Control with Other Business Functions
One of the biggest challenges in quality management is ensuring that quality control data is integrated with other key business functions, such as procurement, inventory management, and production. ERPNext eliminates this siloed approach by providing a fully integrated system. This integration ensures that:
- Quality Control Meets Production Schedules: ERPNext integrates quality checks into production workflows, ensuring that inspections are performed at the right time without disrupting production.
- Inventory and Quality Data Sync: Track both inventory and quality data simultaneously, so if a batch fails to meet quality standards, you can easily trace the faulty batch back to its raw materials and production process.
With manufacturing ERP software, businesses in the ceramic and faucet industry can ensure that quality control becomes an integral part of their overall operational strategy.
Key Features of ERPNext for Ceramic and Faucet Industry Quality Management
ERPNext offers a range of features designed specifically for improving quality management in the ceramic and faucet industries. Let’s explore these features in more detail:
1. Real-Time Monitoring and Alerts
ERP for manufacturing industry businesses must stay on top of quality control throughout production. ERPNext’s real-time monitoring capabilities ensure that managers can:
- Set up quality control alerts that notify relevant teams when quality issues are detected, allowing for faster response times and corrective actions.
- Track quality metrics over time, helping businesses identify trends, such as frequent defects at specific stages in the production process.
These real-time capabilities help prevent quality issues from escalating into larger problems, keeping production moving smoothly and cost-effectively.
2. Customizable Quality Control Plans
Every manufacturer in the ceramic and faucet industry has unique needs when it comes to quality management. ERPNext allows for customizable quality control plans that can be tailored to specific production processes. This means that manufacturers can:
- Create quality control checklists based on the specific requirements of each product or production line.
- Set thresholds for acceptable quality levels, ensuring that only products that meet those standards are allowed to proceed to the next phase.
- Incorporate automated quality checks at different stages, such as before firing ceramics or after the assembly of faucets.
3. Reporting and Documentation
Compliance with industry standards and regulations is a critical concern in manufacturing, especially for the ceramic and faucet industries. ERPNext makes it easy to generate detailed reports, including:
- Compliance Reports: Ensure that all products meet local and international quality regulations.
- Audit Trails: ERPNext maintains a complete record of all quality-related activities, helping businesses comply with audits and demonstrate due diligence in quality control processes.
- Defect Tracking Reports: Track defects across products, identify root causes, and implement corrective actions, improving the overall quality of your manufacturing processes.
With ERP quality management integrated into the system, businesses can generate reports that demonstrate their commitment to quality and compliance.
Case Studies: How ERPNext Improves Quality Management in Ceramic and Faucet Industries
Case Study 1: Ceramic Manufacturer Enhancing Product Quality
A ceramic tile manufacturer struggled with managing quality control across multiple production lines. Quality issues were not being identified early enough, leading to high levels of scrap and waste. After implementing ERPNext’s quality management module, the company was able to:
- Perform automated quality checks at each stage of production.
- Track defects and identify trends, which allowed them to take corrective actions earlier in the production cycle.
- Improve product quality, reduce waste, and lower production costs by 25% within the first quarter of implementation.
Case Study 2: Faucet Manufacturer Reducing Defects
A faucet manufacturer faced challenges with inconsistent quality in their products, leading to customer complaints and returns. Using ERPNext, the company was able to:
- Set up quality control checkpoints at every stage of production, from sourcing materials to final assembly.
- Track the performance of each product batch and take corrective action whenever defects were identified.
- Cut the defect rate by 30% in the first six months, while also improving customer satisfaction and reducing returns.
Both case studies show how ERPNext’s quality management module can help ceramic and faucet manufacturers improve product quality, reduce waste, and enhance customer satisfaction.
How to Choose the Right ERP System for Your Ceramic and Faucet Business
Selecting the right ERP for Ceramic and Faucet Industry is a crucial decision that can significantly impact your business’s operations. Here are some key factors to consider when choosing an ERP system:
- Industry-Specific Features: Ensure the ERP system includes specialized modules for quality management, inventory tracking, and manufacturing processes specific to the ceramic and faucet industry.
- Scalability: Choose an ERP system that can grow with your business, handling an increasing volume of production and complexity.
- Ease of Use: Ensure the ERP system is user-friendly and can be easily adopted by your team without extensive training.
- Integration: Ensure the ERP system integrates smoothly with other tools you use, such as procurement, inventory, and accounting software.
Implementation Tips for ERP Solutions in Ceramic and Faucet Industry
Successfully implementing ERP software in your ceramic or faucet business requires careful planning. Here are some tips for a smooth implementation:
- Set Clear Objectives: Define the specific goals you want to achieve with the ERP system, such as improving product quality or streamlining production workflows.
- Engage Key Stakeholders: Involve key personnel from manufacturing, quality control, and finance departments to ensure the system meets all requirements.
- Training and Support: Provide adequate training to your team to ensure they can effectively use the new system.
- Monitor and Optimize: Continuously monitor the system’s performance and make adjustments as needed to optimize workflows and improve results.
Conclusion: Revolutionize Quality Management with ERPNext
For ceramic and faucet businesses, effective quality management is essential to maintaining a competitive edge. ERP for Ceramic and Faucet Industry with ERPNext offers a comprehensive solution that integrates quality control with other key business functions, including production, inventory, and finance. By using ERPNext, businesses can streamline their quality management processes, reduce defects, improve product quality, and enhance overall efficiency.
At Sigzen Technologies, we specialize in ERPNext implementation for manufacturing industries, ensuring that your business can fully leverage the benefits of ERP. Ready to improve quality management in your ceramic or faucet business? Request a demo today and experience the power of ERPNext firsthand.