SigzenMETAL is a specialized ERP solution developed by Sigzen Technologies, built on the robust ERPNext platform, specifically designed to meet the complex needs of the metal industry. SigzenMETAL offers advanced features to streamline processes, optimize resource allocation, and enhance quality control, all while simplifying subcontracting workflows. By integrating critical manufacturing functions and improving visibility across operations, SigzenMETAL helps metal manufacturers boost efficiency, reduce costs, and maintain high-quality standards within a single, unified platform—whether you’re managing custom metal products or large-scale industrial manufacturing.
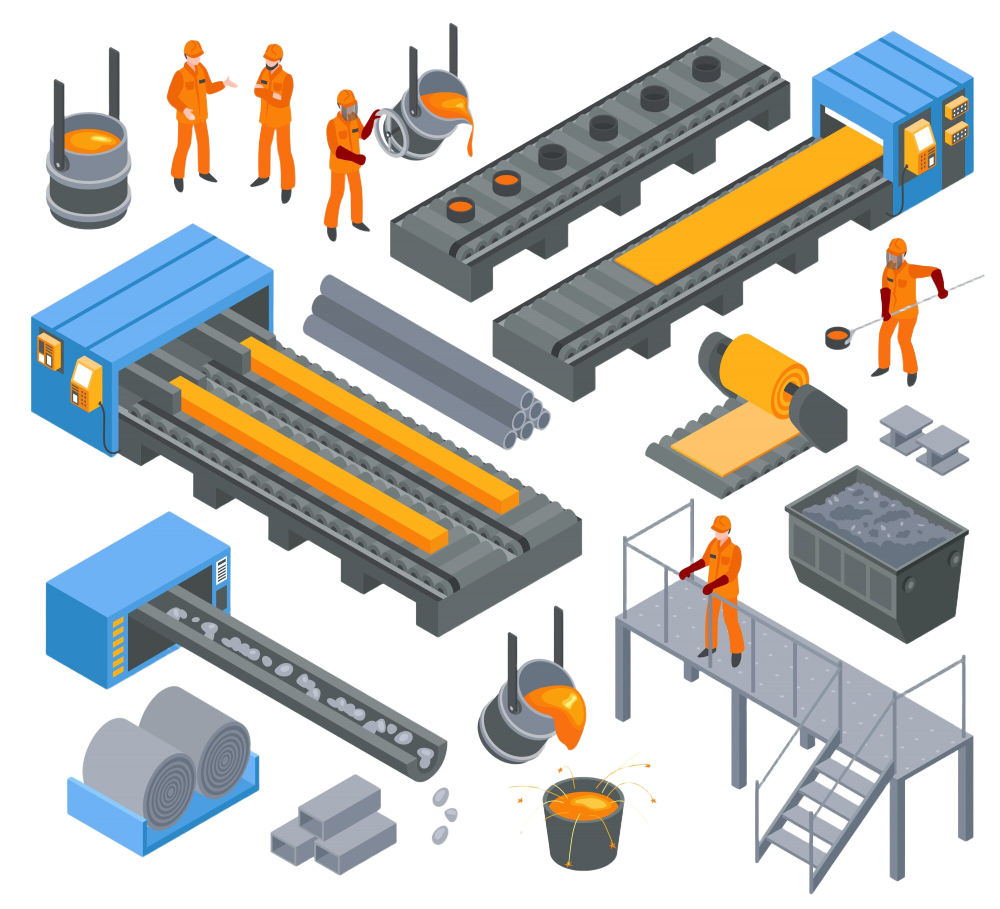
Key Features
1. Asset and Workstation Integration
Streamlined Operations
Link assets and tools directly with workstations to enhance manufacturing efficiency.
Precise Resource Allocation
Assign tools and assets to specific operations in the manufacturing cycle for optimized resource utilization.
Accurate Cost allocation of tools
Accurately allocate tool and assets cost to the manufactured goods for better cost management.
2. Advanced Subcontracting Workflow
Configurable Subcontracting at BOM Level
Customize subcontracting workflows by selecting operations for subcontracting directly within the Bill of Materials (BOM).
Seamless Material Transfers
Effortlessly transfer raw materials to job worker warehouses during subcontracting order creation.
Consolidated Orders
Create a single subcontracting order for multiple job cards, reducing administrative overhead.
Automation
Automatically complete job cards when subcontracted items are received and auto stock entries creation
3. Comprehensive Quality Control (QC) and Testing
Automated QC Creation
Generate QC records automatically upon job card completion or pausing.
Scrap and Partial Completion Tracking
Record scrap and completed quantities in real-time for paused job cards.
Dynamic Job Progression
Enable the next job card to start when partial quantities are produced and tested.
Scalable QC Forms
Create QC forms for more than 10 items and manage multiple readings for a single item with ease.
Bulk Autofill
Save time by auto-filling item readings based on test results.
Rework Workflow
Handle rework seamlessly for rejected quantities at both QC and work order levels.
Scrap Management
Manage scrap and re-use of scrape with extra added process cost, this will allow tracking accurate costing of manufacturing including scrap processing cost.
4. Enhanced Job Card Functionality
Asset and Tool Availability Checks
Prevent job card initiation if essential tools and assets are unavailable.
Timelog Management
Maintain detailed logs for tool and asset usage.
Tool & Asset Flexibility
Mark tool transfers, asset repairs, maintenance, and movement directly within the Job Card interface.
Inspection Compliance
Restrict job card submission if quality inspections or subcontracting cycles are incomplete, ensuring workflow integrity.
5. Reports and dashboards
Job Card Status and Progress Report
Offers a comprehensive view of each job card’s status and progress,accepted and rejected quantity, asset and tool usage essential for daily operations management.
Production Forecast Report
Tracks upcoming manufacturing schedules with expected completion dates based on open Work Orders and Sales Orders. Useful for production planning.
Employee Production Efficiency
Evaluates individual employee efficiency by comparing actual output vs. expected output. Helps in performance analysis and workforce optimization.
Scrap Variance
Compares actual scrap generated during manufacturing against the expected scrap as per BOM. Helps in identifying excessive material wastage.
Integration With Other ERPNext Modules
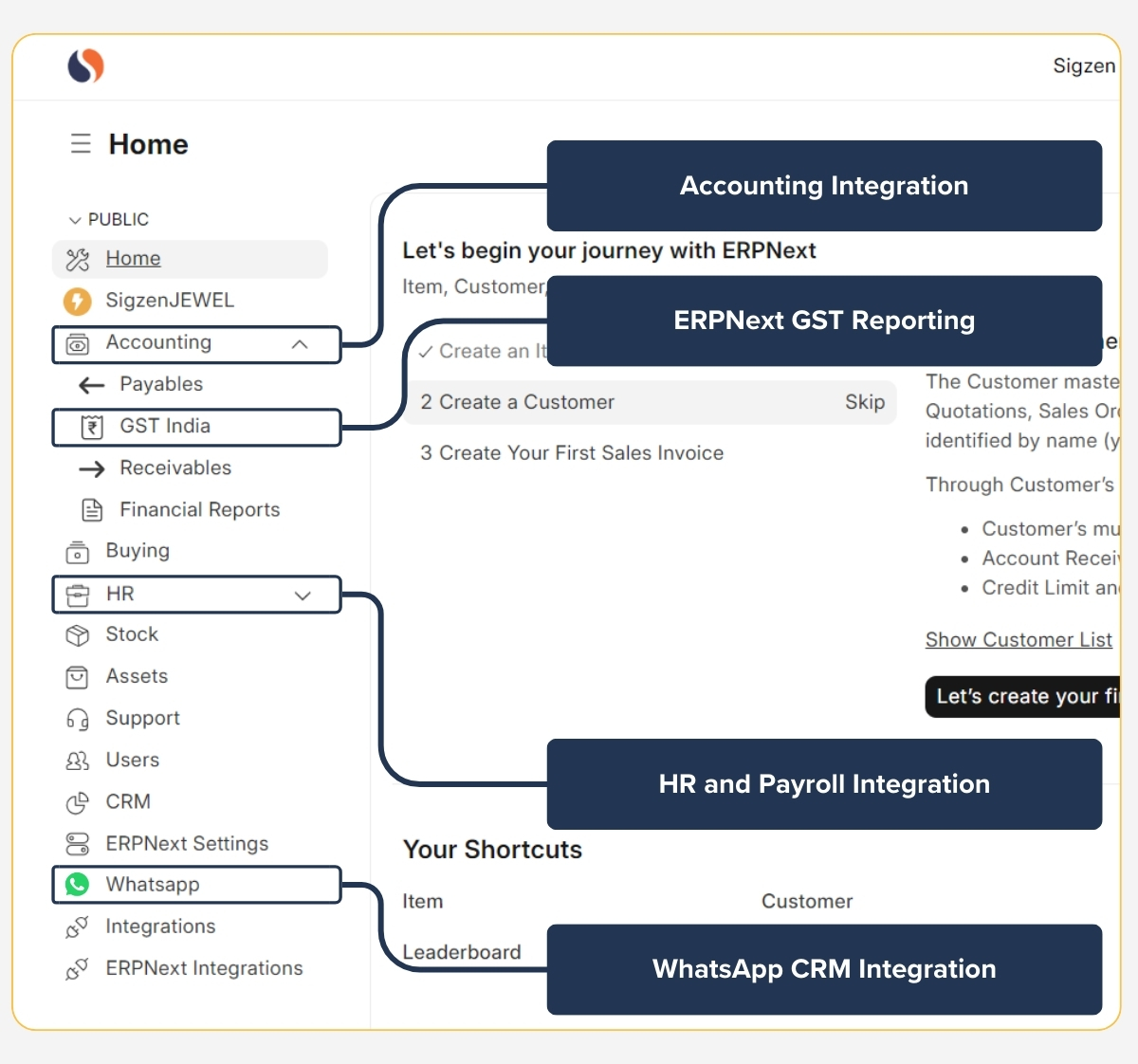
Frequently Asked Questions
How can SigzenMETAL benefit metal industry businesses?
SigzenMETAL enhances operational efficiency by automating key processes like inventory tracking, production planning, and sales management. It reduces manual errors, improves resource utilization, and provides real-time insights to help businesses make data-driven decisions and increase profitability.
How does SigzenMETAL improve inventory management?
SigzenMETAL offers real-time tracking of raw materials and finished goods, optimizing stock levels and reducing waste. Its advanced inventory management features ensure accurate order fulfilment and efficient resource utilization.
Can SigzenMETAL handle complex production processes?
Yes, SigzenMETAL is equipped to manage intricate production workflows, including batch processing, job scheduling, and machine maintenance. It ensures seamless coordination between departments, leading to improved production efficiency.
Is SigzenMETAL customizable to specific business needs?
Absolutely. SigzenMETAL is built on a flexible platform that allows customization to align with unique business requirements, ensuring the solution adapts to your specific operational processes.
What kind of support and training does Sigzen provide for SigzenMETAL users?
Sigzen offers comprehensive support, including initial setup assistance, user training sessions, and ongoing technical support to ensure your team can effectively utilize SigzenMETAL to its fullest potential.
Begin Your ERP Journey with a Free Consultation
Optimize your metal operations with SigzenMETAL. Contact us today for a demo and discover how our solution can streamline logistics, automate sales processes, and boost overall efficiency.