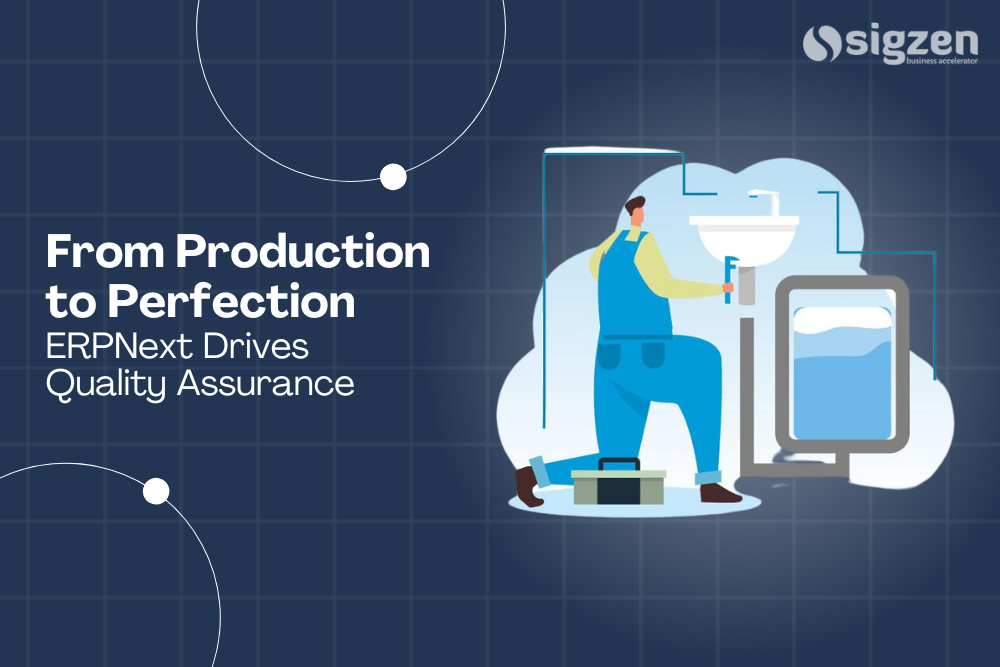
The faucets manufacturing industry requires specialized solutions to ensure efficiency and maintain high-quality standards. ERPNext, a comprehensive ERP software, integrates various business processes into a single cohesive system. It offers real-time inventory management for monitoring stock levels and managing raw materials and finished products efficiently. Streamlined production planning tools ensure organized manufacturing processes, while advanced quality control features enable inspections at various production stages to ensure high-quality products.
ERPNext’s integrated supply chain management module helps manage suppliers, track shipments, and ensure timely delivery of raw materials, enhancing collaboration and minimizing disruptions. Its robust financial management tools cover budgeting, expense tracking, financial reporting, and analysis, providing accurate financial data for informed decision-making. The CRM module helps manage customer interactions, track sales leads, and improve customer satisfaction, fostering long-term relationships and increased sales. Real-time reporting and analytics tools provide insights into operations, enabling data-driven decisions to optimize processes, reduce costs, and improve overall efficiency. With its comprehensive features, ERPNext is the ideal solution for faucets businesses looking to enhance efficiency and maintain high-quality standards.
Sigzen Technologies, a leading ERPNext consultant, has played a pivotal role in implementing ERPNext for faucets businesses. With expertise in ERPNext customization and development, Sigzen Technologies provides tailored solutions to meet the specific needs of faucet manufacturers. Their services include ERPNext implementation, training, support, customization, and integration. By leveraging these services, faucets businesses can optimize their processes and achieve greater efficiency.
1.Integrated Quality Management Module
ERPNext provides a comprehensive quality management module that integrates seamlessly with manufacturing processes, ensuring that every step of production is monitored for quality compliance. This integration allows for real-time quality checks and tracking, which significantly reduces the chances of defective products reaching the market. Customizable quality checklists and parameters ensure that specific quality standards are consistently maintained across all production batches, enhancing overall product quality. The module also facilitates the creation of detailed quality reports that can be used for continuous improvement and audit purposes. This integrated quality management module is part of the ERPNext for Faucets Business service provided by Sigzen Technologies.
- Comprehensive Integration: ERPNext integrates quality management seamlessly with manufacturing processes, ensuring every step adheres to industry-specific quality standards, enhancing overall product reliability.
- Real-Time Monitoring: The system enables real-time quality checks and tracking, significantly reducing the chances of defective products and allowing for immediate corrective actions tailored to the faucets industry.
- Customizable Checklists: Customizable quality checklists and parameters ensure consistent adherence to industry-specific quality standards across all batches, tailoring the quality processes to the unique requirements of the faucets industry.
2.Automated Inspection and Testing
The system automates inspection and testing procedures, ensuring that all faucets undergo rigorous quality checks before they reach the market. Automated alerts and notifications are generated for any deviations from quality standards, enabling quick corrective actions. Detailed inspection reports and testing logs are maintained for audit purposes and continuous improvement, fostering a culture of accountability and quality. These automated processes reduce manual intervention, minimizing human error and speeding up the production cycle. Automated inspection and testing are essential features of ERPNext for Faucets Business offered by Sigzen Technologies.
- Inspection Automation: ERPNext automates inspection and testing procedures specific to the faucets industry, ensuring rigorous quality checks for all products before market release, thus minimizing human error.
- Real-Time Alerts: Automated alerts and notifications for quality deviations enable quick corrective actions, preventing defects and maintaining product integrity, ensuring adherence to industry standards.
- Detailed Documentation: The system maintains detailed inspection reports and testing logs for audit purposes and continuous improvement, providing a robust quality management system tailored to industry needs.
3.Supplier Quality Assurance
ERPNext helps maintain high-quality standards by ensuring that raw materials from suppliers meet predefined quality criteria. Supplier quality tracking and performance evaluation are facilitated through regular audits and feedback mechanisms. Integration with supplier management modules ensures that only certified suppliers are used, reducing the risk of quality issues from the source. The system also supports the evaluation and re-evaluation of suppliers based on their performance, ensuring a reliable supply chain. Supplier quality assurance is a critical component of the ERPNext for Faucets Business service provided by Sigzen Technologies.
- Quality Standards: ERPNext ensures raw materials from suppliers meet predefined industry-specific quality criteria, maintaining high standards from the very beginning of the supply chain.
- Supplier Audits: Regular audits and feedback mechanisms facilitate supplier quality tracking and performance evaluation, ensuring consistent material quality in line with industry expectations.
- Certified Suppliers: Integration with supplier management modules ensures only certified suppliers are used, reducing quality issues and fostering reliable supplier relationships within the industry.
4.Batch and Serial Number Tracking
The system supports batch and serial number tracking, enabling precise tracking of individual faucet components and finished products. This feature aids in traceability, allowing manufacturers to quickly identify and rectify issues in specific batches. It also facilitates effective recall management if any quality issues are detected post-production, ensuring customer safety and trust. Additionally, this tracking helps in maintaining accurate inventory records, which is crucial for efficient stock management. Batch and serial number tracking is a valuable feature included in the ERPNext for Faucets Business solution by Sigzen Technologies.
- Precise Tracking: ERPNext supports batch and serial number tracking, enabling precise tracking of individual components and finished products, crucial for quality control in the faucets industry.
- Effective Recall Management: Facilitates effective recall management if quality issues are detected, ensuring customer safety and trust through transparent and efficient handling specific to industry standards.
- Inventory Management: Enhanced traceability improves inventory management and reduces waste, contributing to cost savings and operational efficiency by ensuring only high-quality components are used.
5.Non-Conformance Management
ERPNext provides robust non-conformance management tools to document, analyze, and resolve quality issues. Non-conformances are recorded and classified, with root cause analysis tools available to prevent recurrence. Corrective and preventive actions (CAPA) are tracked within the system, ensuring continuous quality improvement and compliance with industry standards. This systematic approach to managing non-conformances helps in minimizing production losses and maintaining product integrity. Non-conformance management is a significant aspect of the ERPNext for Faucets Business service offered by Sigzen Technologies.
- Issue Documentation: ERPNext documents, analyzes, and resolves quality issues with robust non-conformance management tools, ensuring all issues are tracked and addressed in line with industry standards.
- Root Cause Analysis: Non-conformances are recorded and classified with root cause analysis tools to prevent recurrence, promoting a culture of continuous improvement tailored to the faucets industry.
- CAPA Tracking: Corrective and preventive actions (CAPA) are tracked within the system, ensuring continuous quality improvement and compliance with industry standards, reducing future non-conformances.
6.Real-Time Quality Monitoring
Real-time data collection and monitoring capabilities allow for continuous quality assessment during production. Dashboards and reports provide insights into quality metrics, helping management make informed decisions. Immediate feedback loops enable quick adjustments to processes, maintaining high-quality standards and minimizing production downtime. These real-time insights facilitate proactive decision-making, preventing potential quality issues before they escalate. Real-time quality monitoring is a key feature of the ERPNext for Faucets Business solution provided by Sigzen Technologies.
- Continuous Assessment: Real-time data collection and monitoring capabilities allow continuous quality assessment during production, ensuring immediate identification of potential issues in the faucets industry.
- Quality Metrics: Dashboards and reports provide insights into quality metrics, helping management make informed decisions to maintain high production standards specific to industry needs.
- Immediate Feedback: Immediate feedback loops enable quick adjustments to processes, maintaining high-quality standards and minimizing production downtime, leading to consistent product quality.
7.Quality Audit and Compliance
ERPNext facilitates regular quality audits to ensure compliance with industry standards and regulations. Comprehensive audit trails and documentation support internal and external audits. The system ensures that all quality-related documentation is maintained and easily accessible for regulatory compliance, safeguarding the company’s reputation and market position. By streamlining the audit process, the system helps in identifying areas of improvement and ensuring adherence to best practices. Quality audit and compliance are integral parts of the ERPNext for Faucets Business service by Sigzen Technologies.
- Regular Audits: ERPNext facilitates regular quality audits to ensure compliance with industry standards and regulations, safeguarding the company’s reputation in the faucets industry.
- Audit Trails: Comprehensive audit trails and documentation support internal and external audits, providing transparent and accountable records in line with industry requirements.
- Regulatory Compliance: The system ensures all quality-related documentation is maintained and accessible for regulatory compliance, helping the company stay ahead in quality assurance and industry standards.
8.Calibration and Maintenance of Equipment
The system manages the calibration and maintenance schedules of manufacturing equipment to ensure consistent quality output. Alerts and reminders for equipment calibration and maintenance activities prevent potential quality issues due to equipment malfunction. Detailed records of calibration and maintenance activities help in compliance and quality assurance, ensuring that equipment performance remains optimal. This proactive approach to equipment maintenance reduces downtime and extends the lifespan of machinery. Calibration and maintenance of equipment are supported by the ERPNext for Faucets Business service from Sigzen Technologies.
- Schedule Management: ERPNext manages calibration and maintenance schedules of manufacturing equipment for consistent quality output, preventing equipment-related defects specific to the faucets industry.
- Preventive Alerts: Alerts and reminders for calibration and maintenance activities prevent potential quality issues by ensuring equipment is always in optimal condition.
- Detailed Records: Detailed records of calibration and maintenance activities help in compliance and quality assurance, providing a historical log of equipment performance tailored to industry standards.
9.Quality Documentation and Standard Operating Procedures (SOPs)
ERPNext manages and maintains all quality-related documentation, including SOPs, work instructions, and quality manuals. Controlled document management ensures that only the latest versions of documents are used in production. Easy access to quality documentation supports consistent adherence to quality standards, reducing errors and improving operational efficiency. The system also facilitates the creation and revision of SOPs, ensuring that all processes are up-to-date and effective. Quality documentation and SOPs management are essential features of the ERPNext for Faucets Business solution by Sigzen Technologies.
- Document Management: ERPNext manages and maintains all quality-related documentation, including SOPs, work instructions, and quality manuals, ensuring easy access and control tailored to industry standards.
- Version Control: Controlled document management ensures only the latest versions of documents are used in production, reducing errors and miscommunications.
- Consistent Standards: Easy access to quality documentation supports consistent adherence to quality standards, enhancing operational efficiency and reducing variability specific to the faucets industry.
10.Continuous Improvement and Quality Metrics
ERPNext supports continuous improvement initiatives through detailed quality metrics and performance indicators. Key quality metrics are tracked and analyzed to identify trends and areas for improvement. The system facilitates Kaizen, Six Sigma, and other quality improvement methodologies, driving ongoing enhancement of manufacturing processes and ensuring that the company remains competitive and innovative. By promoting a culture of continuous improvement, the system helps in achieving long-term business success. Continuous improvement and quality metrics are critical aspects of the ERPNext for Faucets Business service offered by Sigzen Technologies.
- Quality Metrics: ERPNext supports continuous improvement initiatives through detailed quality metrics and performance indicators, driving ongoing process enhancements tailored to industry needs.
- Improvement Methodologies: Facilitates Kaizen, Six Sigma, and other quality improvement methodologies for systematic and sustained improvements in quality.
- Market Adaptation: Ensures high-quality standards and adaptation to changing market demands and technological advancements, keeping the company competitive and innovative within the faucets industry.
ERPNext is a powerful tool for faucets manufacturers looking to enhance their quality control and streamline their operations. With features like comprehensive inventory management, efficient production planning, enhanced quality control, seamless supply chain management, and robust financial management, ERPNext offers a holistic solution for the faucets industry. Sigzen Technologies, with its expertise in ERPNext implementation and customization, ensures that faucets businesses can achieve their operational goals and drive growth.