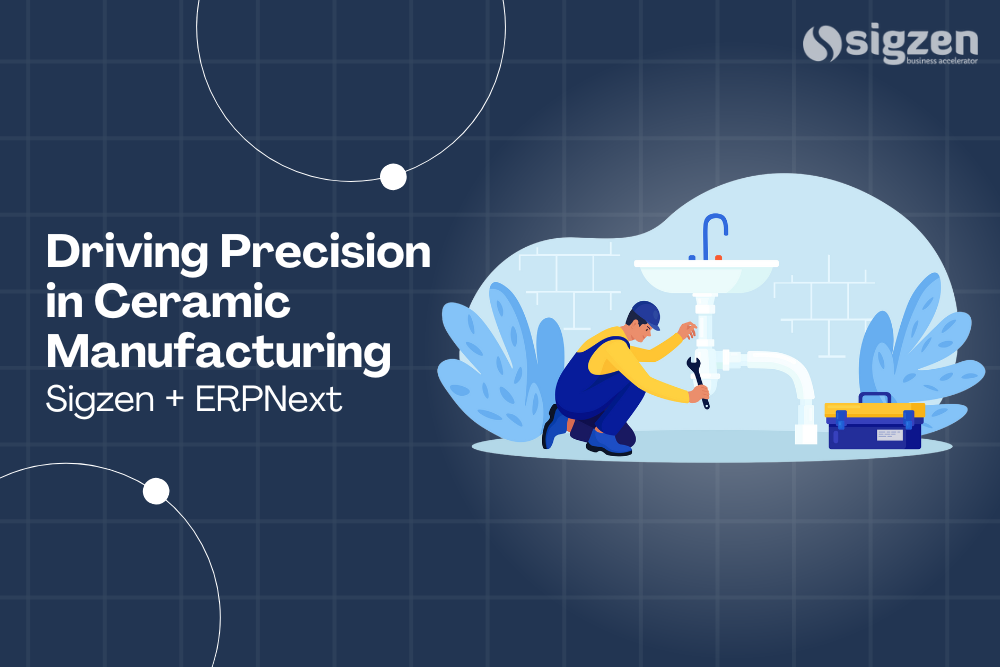
Introduction: Revolutionizing Ceramic Manufacturing with ERPNext
The ceramic industry is synonymous with precision, efficiency, and quality. From creating intricate designs to scaling mass production, ceramic manufacturers face unique challenges in maintaining inventory levels, optimizing workflows, and ensuring consistent quality. Traditional systems often fall short in meeting these dynamic requirements. Enter ERP for Ceramic Industry—a transformative solution that integrates production, inventory, and quality management into a unified platform.
ERPNext, offered by Sigzen, provides comprehensive tools to enable real-time production planning, streamline inventory management, and enhance operational efficiency. In this article, we explore how ERPNext addresses critical pain points in the ceramic manufacturing process, highlighting its benefits for small and large businesses alike.
Challenges in Ceramic Manufacturing
1. Complex Production Processes
Producing ceramic items involves multiple steps, including molding, glazing, and firing, all requiring precise coordination.
2. Inventory Management
Raw materials like clay, glaze, and pigments must be available in the right quantities, and finished goods need effective storage and tracking.
3. Quality Assurance
Maintaining consistent quality is essential to meet customer expectations and regulatory standards.
4. Resource Allocation
Efficiently allocating resources like labor, machines, and materials can be challenging without real-time visibility.
5. Scalability
Small businesses often struggle to scale operations due to inefficient systems and manual processes.
How ERPNext Enhances Production Planning for the Ceramic Industry
1. Real-Time Production Management
ERPNext integrates production planning and execution, ensuring seamless coordination across departments. Key features include:
- Work Order Management: Create and manage work orders for every stage of the production process.
- Production Scheduling: Optimize schedules to minimize downtime and ensure timely completion of orders.
- Progress Tracking: Monitor production progress in real-time to identify and resolve bottlenecks.
Explore ERPNext’s production management module.
2. Streamlined Inventory Management
Effective inventory control is crucial for reducing costs and avoiding production delays. ERPNext offers:
- Stock Inventory Management Software: Track raw materials and finished goods in real-time.
- Batch and Serial Number Tracking: Ensure traceability of materials and products across the supply chain.
- Automated Reordering: Set minimum stock levels to trigger automatic purchase requests.
Learn more about ERPNext’s inventory features.
3. Quality Control Integration
Consistent product quality is vital in the ceramic industry. ERPNext helps ensure quality through:
- Inline Quality Inspections: Perform quality checks at every stage of production, from raw materials to final products.
- Non-Conformance Management: Identify and address defects promptly.
- Audit Trails: Maintain detailed records for compliance and continuous improvement.
Discover ERPNext’s quality management capabilities.
4. Advanced Resource Optimization
With ERPNext, manufacturers can allocate resources more effectively:
- Machine Utilization: Monitor machine performance and schedule maintenance to avoid downtime.
- Labor Allocation: Assign tasks based on employee skills and availability.
- Material Planning: Ensure raw materials are available when needed to avoid production delays.
5. Scalability for Small and Large Businesses
ERPNext is highly adaptable, making it suitable for businesses of all sizes:
- Manufacturing Software for Small Business: Affordable pricing and modular features make ERPNext accessible to smaller manufacturers.
- Scalability for Growing Enterprises: As businesses expand, ERPNext scales to accommodate increased production volumes and complexity.
Key Features of ERP Software for Manufacturing Industry
1. Comprehensive Dashboards
Gain a real-time overview of production, inventory, and sales with customizable dashboards.
2. Automated Workflows
Reduce manual effort by automating processes like purchase requests, stock transfers, and quality checks.
3. Analytics and Reporting
Generate detailed reports on production efficiency, inventory turnover, and quality metrics to drive data-driven decisions.
4. Multi-Warehouse Management
Manage inventory across multiple locations with ease.
5. Mobile Accessibility
Access ERP features from any device, enabling on-the-go management.
ERPNext Benefits for Ceramic Manufacturers
1. Reduced Operational Costs
- Optimize resource utilization and minimize waste to save costs across production and inventory management.
2. Enhanced Productivity
- Automation of repetitive tasks and real-time insights improve overall efficiency and output.
3. Improved Quality Assurance
- Integrated quality control processes ensure consistent product quality and compliance with standards.
4. Better Decision-Making
- Access to real-time data empowers managers to make informed decisions and respond swiftly to challenges.
5. Scalability and Flexibility
- ERPNext grows with your business, offering flexibility to adapt to changing demands.
Real-World Impact: ERPNext in Ceramic Manufacturing
Challenge: A mid-sized ceramic tile manufacturer struggled with manual production scheduling, inventory tracking errors, and inconsistent quality control.
Solution: After implementing ERPNext, the company achieved:
- 20% improvement in production efficiency through automated scheduling.
- 30% reduction in inventory carrying costs due to real-time tracking.
- Enhanced quality control with fewer defects and improved customer satisfaction.
Request a demo from Sigzen to see how ERPNext can transform your ceramic manufacturing operations.
Future Trends in Ceramic Manufacturing with ERPNext
1. Sustainable Practices
ERPNext can track and report on resource usage, helping manufacturers adopt eco-friendly practices like waste reduction and energy efficiency.
2. IoT Integration
Integrating IoT sensors with ERPNext enables real-time monitoring of equipment and production conditions.
3. Predictive Analytics
Leverage AI-driven insights to forecast demand, optimize inventory, and improve production planning.
4. Customization
ERPNext offers modular features that can be tailored to meet the specific needs of ceramic manufacturers.
Best Practices for Implementing ERP in the Ceramic Industry
- Identify Key Objectives: Define your goals, such as reducing costs or improving quality control, to ensure the ERP system aligns with your needs.
- Engage Key Stakeholders: Involve team members from production, inventory, and finance in the implementation process.
- Ensure Data Accuracy: Clean and organize data before migrating to the ERP system.
- Provide Training: Equip employees with the skills to use ERPNext effectively.
- Monitor KPIs: Track metrics like production cycle times, defect rates, and inventory turnover to measure success.
Conclusion: Transforming Ceramic Manufacturing with ERPNext
Efficient production planning and inventory management are essential for success in the ceramic industry. ERP for Ceramic Industry, powered by ERPNext, offers a comprehensive solution to streamline operations, improve quality, and reduce costs. Whether you’re a small business looking for affordable manufacturing software for small business or a large enterprise seeking advanced tools, ERPNext adapts to your needs and ensures sustainable growth.
Ready to optimize your ceramic manufacturing processes? Request a demo from Sigzen today!