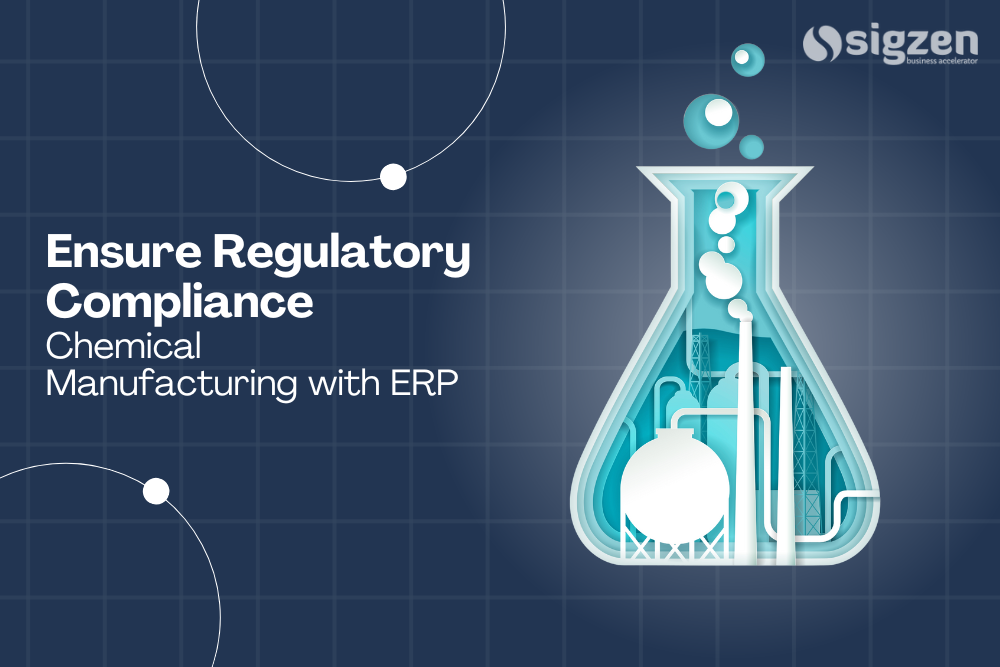
Introduction: Simplifying Compliance with ERP for the Chemical Industry
Chemical manufacturing is one of the most regulated industries globally, with stringent compliance standards that require meticulous tracking of processes, materials, and quality metrics. For businesses, adhering to these regulations can be daunting without the right tools. Enter ERP for Chemical Manufacturing—a robust solution that not only streamlines operations but also ensures compliance with industry standards and governmental regulations.
Whether it’s maintaining Material Safety Data Sheets (MSDS), tracking hazardous materials, or automating quality checks, ERP software tailored for the chemical industry offers a comprehensive approach to staying compliant while boosting productivity. Let’s explore how ERP systems transform chemical manufacturing compliance and operational efficiency.
Why Compliance is Critical in Chemical Manufacturing
Chemical manufacturing deals with sensitive materials and processes that pose potential risks to the environment, workforce, and consumers. Regulatory frameworks such as REACH, OSHA, and EPA in the USA and GHS globally impose strict guidelines that manufacturers must follow.
Key compliance challenges include:
- Maintaining Accurate Documentation: Proper record-keeping for audits and certifications.
- Ensuring Product Traceability: Tracking raw materials, batches, and finished goods.
- Managing Hazardous Materials: Safe handling, labeling, and disposal.
- Quality Assurance: Meeting industry-specific standards for product quality.
Failure to comply can lead to hefty fines, operational shutdowns, or damage to brand reputation. This makes ERP software indispensable for achieving compliance in the chemical industry.
How ERP Software Enhances Compliance in Chemical Manufacturing
1. Centralized Documentation and Reporting
An ERP system consolidates all regulatory documents into a single platform, making it easier to manage, retrieve, and update them as needed.
- Automated Reports: Generate compliance reports in real time for audits and inspections.
- Document Management: Maintain MSDS, certifications, and inspection logs in a digital, searchable format.
- Audit Trails: Track changes and maintain a log of activities for accountability.
With ERP systems like ERPNext, manufacturers can quickly generate reports for compliance audits, saving time and reducing errors.
2. Enhanced Quality Control
Quality control is a cornerstone of compliance in chemical manufacturing. ERP software integrates quality checks at every stage of production.
- Automated Quality Inspections: Implement automated checks for raw materials, in-process goods, and finished products.
- Non-Conformance Management: Identify and resolve quality issues promptly.
- Regulatory Standards Integration: Ensure compliance with ISO, GHS, and other quality standards.
For example, the Quality Management module of ERPNext allows manufacturers to define quality parameters and automate inspection points, ensuring consistency and compliance.
3. Material Tracking and Traceability
Tracking hazardous materials from procurement to disposal is essential for regulatory compliance. ERP systems provide end-to-end traceability:
- Batch Tracking: Monitor every batch of raw material and its usage in finished products.
- Real-Time Inventory Visibility: Identify the location and status of hazardous materials at all times.
- Labeling and Safety Standards: Ensure accurate labeling and proper documentation for transport.
This level of traceability minimizes risks and ensures adherence to safety and environmental regulations, making ERP systems like SigzenChem indispensable.
4. Compliance with Safety and Environmental Regulations
ERP systems help manage safety data and environmental compliance effortlessly:
- Safety Data Sheet Management: Automate the updating and distribution of MSDS.
- Waste Management: Track hazardous waste disposal in compliance with environmental laws.
- Incident Reporting: Document and analyze workplace incidents to prevent future occurrences.
For example, the SigzenChem ERP solution includes features to manage compliance with OSHA and EPA standards, making it easier for manufacturers to maintain workplace safety.
5. Streamlined Supply Chain and Procurement
Regulatory compliance extends to suppliers and procurement. ERP systems ensure that every step in the supply chain adheres to regulations:
- Vendor Compliance Management: Evaluate and onboard suppliers based on compliance standards.
- Procurement Automation: Ensure that purchased materials meet regulatory specifications.
- Supplier Traceability: Maintain records of supplier certifications and compliance documentation.
The Purchase Cycle module in ERPNext simplifies supplier management, ensuring regulatory alignment across the supply chain.
Key Features of ERP for the Chemical Industry
A robust ERP system tailored for chemical manufacturing offers several key features to enhance compliance:
- Regulatory Compliance Management: Built-in tools for tracking and ensuring adherence to local and global regulations.
- Real-Time Data Insights: Dashboards and analytics for monitoring compliance metrics.
- Risk Management: Tools to identify, assess, and mitigate risks in production and supply chain.
- Production Planning: Ensure production processes meet quality and regulatory standards.
- Integrated Quality Management: Automated workflows for quality checks and non-conformance tracking.
Benefits of ERP for Chemical Manufacturing Compliance
1. Reduced Regulatory Risks
ERP systems minimize the risk of non-compliance by automating tracking and reporting processes, ensuring no detail is overlooked.
2. Improved Operational Efficiency
By centralizing data and automating workflows, ERP systems reduce the time and effort spent on compliance-related tasks.
3. Enhanced Decision-Making
Real-time data provides insights into compliance and operational performance, enabling manufacturers to make informed decisions quickly.
4. Cost Savings
Avoiding regulatory penalties and optimizing processes lead to significant cost reductions over time.
5. Competitive Advantage
A compliant, efficient operation enhances brand reputation and positions manufacturers as industry leaders.
Case Study: SigzenChem ERP in Action
A mid-sized chemical manufacturer implemented SigzenChem ERP to address compliance and operational challenges. Results included:
- 30% Reduction in Compliance Costs: Automated processes reduced manual intervention.
- 20% Increase in Quality Consistency: Integrated quality checks ensured adherence to standards.
- Faster Audits: Centralized documentation reduced audit preparation time by 50%.
Learn more about SigzenChem ERP’s capabilities.
Best Practices for Implementing ERP in the Chemical Industry
- Assess Compliance Needs: Identify specific regulations and quality standards applicable to your operations.
- Choose the Right Vendor: Opt for ERP solutions like Sigzen.com that specialize in the chemical industry.
- Train Your Team: Ensure employees are proficient in using the ERP system to maximize its potential.
- Monitor and Update: Regularly review ERP data to ensure ongoing compliance and operational efficiency.
Conclusion: The Future of Compliance with ERP for Chemical Manufacturing
Investing in an ERP for the Chemical Industry is no longer optional—it’s a necessity. With features like real-time tracking, automated quality checks, and centralized documentation, ERP systems empower manufacturers to meet regulatory demands effortlessly while improving operational efficiency.
If you’re ready to revolutionize your chemical manufacturing operations, explore Sigzen’s ERP solutions today. Request a demo to experience how Sigzen can simplify compliance and enhance productivity.