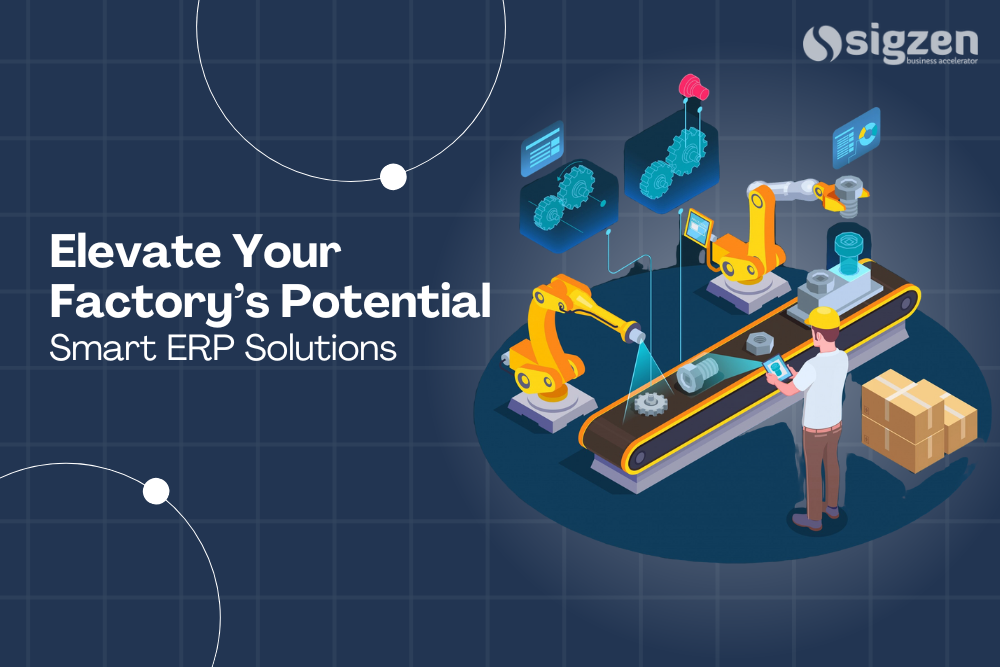
Welcome to ERPNext Manufacturing, where innovation meets excellence in real-time. As an ERPNext expert, I’m excited to guide you through how this solution transforms manufacturing operations. In today’s fast-paced market, businesses need to streamline processes and deliver quality products efficiently. ERPNext Manufacturing offers a comprehensive solution to integrate all aspects of manufacturing into a single platform.
With ERPNext Manufacturing, businesses gain real-time visibility across their entire manufacturing process, empowering decision-makers to adapt quickly to market changes. I’ve seen firsthand how ERPNext Manufacturing optimizes workflows, reduces costs, and improves efficiency.
Sigzen Technologies has played a key role in enhancing ERPNext Manufacturing with innovative solutions tailored to manufacturing needs. Through collaboration, we’ve improved process efficiency and supply chain management. Our expertise in agile manufacturing drives performance and strategic planning. We’re dedicated to unlocking ERPNext Manufacturing’s full potential for businesses worldwide.
1. Bill of Materials (BOM) Management
Allows users to define and manage multi-level BOMs, allowing users to create, maintain, and manage complex multi-level BOM structures. Users can specify raw materials, components, sub-assemblies, and their quantities required for production. With intuitive interfaces, users can easily edit, update, and version BOMs to reflect changes in product designs or manufacturing processes. ERPNext Manufacturing Services by Sigzen Technologies.
- Hierarchical Structure: Define and maintain a structured hierarchy of components and materials required for manufacturing, including raw materials, sub-assemblies, and finished products.
- Revision Management: Easily manage revisions, substitutes, and variants of BOMs to accommodate changes in product design or requirements, ensuring accurate representation of manufacturing processes.
- Cost Analysis: Analyze the cost implications of different BOM configurations, including material costs, labor expenses, and overheads, to optimize production efficiency and profitability.
2.Routing Management
Routing management in ERPNext empowers users to meticulously define the sequence of operations necessary for manufacturing a product. By creating and maintaining routing templates, manufacturers can specify the exact tasks, work centers, and resources required at each production stage. This ensures standardized processes, reduces lead times, optimizes resource allocation, and maintains consistent product quality.the system provides visibility into workflow and dependencies, facilitating accurate scheduling, capacity planning, and cost estimation.ERPNext Manufacturing Services by Sigzen Technologies.
- Standardized Workflows: ERPNext experts implement routing management to standardize production workflows, ensuring consistency and adherence to best practices.
- Improved Efficiency: Clear routing instructions streamline production processes, reducing lead times, minimizing errors, and improving overall efficiency.
- Enhanced Visibility: Routing management provides visibility into the sequence of operations, work center requirements, and dependencies within the manufacturing process, enabling better planning and resource allocation.
3. Production Planning and Scheduling
Enables users to plan production activities, allocate resources efficiently, and create schedules to optimize manufacturing operations. Users can create production schedules based on demand forecasts, resource availability, and production constraints. The system dynamically adjusts schedules to accommodate changes in demand, material availability, or production capacity, ensuring efficient utilization of resources and timely delivery of products.ERPNext Manufacturing Services by Sigzen Technologies.
- Demand Forecasting: Utilize demand forecasts, sales orders, and production plans to create accurate production schedules that align with customer demand and business objectives.
- Capacity Optimization: Optimize production capacity by balancing workload, minimizing idle time, and sequencing tasks to maximize throughput and meet production targets efficiently.
- Adaptive Planning: Respond to changes in demand, resource availability, or production constraints dynamically by adjusting production schedules in real-time, ensuring flexibility and agility in manufacturing operations.
4. Material Requirement Planning (MRP)
Our MRP module automates the generation of procurement and production plans by analyzing demand forecasts, current inventory levels, lead times, and BOMs. By accurately forecasting material requirements, manufacturers can optimize inventory levels, minimize stockouts, and reduce carrying costs. Integration with procurement and inventory modules streamlines the procurement process, ensuring timely availability of materials for production.ERPNext Manufacturing Services by Sigzen Technologies.
- Automated Planning: Automatically generate procurement and production plans based on demand forecasts, current inventory levels, lead times, and BOMs, streamlining the planning process and reducing manual effort.
- Just-in-Time Inventory: Calculate required quantities of raw materials and components to maintain optimal inventory levels, minimizing excess stock while ensuring timely availability to support production schedules.
- Dynamic Adjustments: Continuously adjust procurement and production plans in response to changes in demand, supplier lead times, or production priorities, optimizing resource utilization and minimizing supply chain disruptions.
5. Shop Floor Control
Users gain real-time visibility and control over shop floor activities. Supervisors can monitor work-in-progress, track production status, and allocate resources efficiently to maximize productivity. Task assignment features enable supervisors to delegate work to individual operators, ensuring smooth execution of production processes and adherence to schedules.ERPNext Manufacturing Services by Sigzen Technologies.
- Real-time Monitoring: Monitor production activities on the shop floor in real-time, tracking work-in-progress, resource utilization, and task status to identify bottlenecks and streamline operations.
- Task Assignment: Assign tasks to workers, work centers, or production lines based on priority, skill level, and availability, ensuring efficient utilization of labor and equipment resources.
- Exception Handling: Handle exceptions, delays, or deviations from the planned schedule promptly by adjusting priorities, reallocating resources, or implementing contingency plans to minimize production disruptions.
6. Quality Control
Our Quality Control module enables manufacturers to maintain high product quality standards throughout the production process. Users can define inspection criteria, conduct quality checks at various stages of production, and record inspection results. Non-conformances are promptly identified, documented, and addressed to prevent defective products from reaching customers, thereby enhancing customer satisfaction and brand reputation.ERPNext Manufacturing Services by Sigzen Technologies.
- Standards Enforcement: Define and enforce quality standards throughout the manufacturing process by establishing inspection criteria, quality checkpoints, and acceptance criteria for raw materials, work-in-progress, and finished products.
- Non-conformance Management: Record and manage non-conformances, deviations, or quality issues identified during inspections, initiating corrective actions, and preventive measures to uphold product quality and regulatory compliance.
- Continuous Improvement: Analyze quality data, identify trends, and implement corrective actions to drive continuous improvement in manufacturing processes, enhancing product quality, and customer satisfaction.
7. Inventory Management
ERPNext Manufacturing Services seamlessly integrates with the inventory module to manage raw materials, work-in-progress, and finished goods inventory levels. Users can track stock movements, monitor inventory levels in real-time, and optimize inventory replenishment processes. By maintaining optimal inventory levels, manufacturers can minimize stockouts, reduce carrying costs, and improve overall operational efficiency.ERPNext Manufacturing Services by Sigzen Technologies.
- Inventory Optimization: Optimize inventory levels of raw materials, work-in-progress, and finished goods by leveraging features such as stock reconciliation, warehouse management, and demand forecasting to minimize carrying costs and stockouts.
- Batch and Serial Tracking: Track individual units of inventory through batch and serial number tracking, enabling traceability throughout the supply chain, facilitating recall management, and ensuring compliance with regulatory requirements.
- Multi-location Support: Manage inventory across multiple locations or warehouses, facilitating efficient distribution, replenishment, and transfer of stock to meet customer demand and operational needs.
8. Costing and Accounting Integration
Our solution provides comprehensive costing and accounting integration to accurately calculate the cost of manufactured items. Material costs, labor expenses, overheads, and other production-related costs are automatically captured and allocated to products, enabling accurate cost analysis and profitability tracking. Integration with accounting modules ensures seamless financial reporting and compliance with accounting standards.ERPNext Manufacturing Services by Sigzen Technologies.
- Accurate Cost Calculation: Calculate the total cost of goods manufactured (COGM) accurately by capturing material costs, labor expenses, overheads, and other production-related costs, providing insights into product profitability and cost drivers.
- Integration with Accounting: Integrate manufacturing cost data seamlessly with the accounting system to update inventory valuation, cost of goods sold (COGS), and financial statements, ensuring accurate financial reporting and compliance with accounting standards.
- Cost Analysis: Analyze manufacturing costs at various levels of granularity, such as by product, batch, or work order, to identify cost-saving opportunities, optimize pricing strategies, and improve overall profitability.
9. Resource Management
Helps manufacturers effectively manage and optimize manufacturing resources such as equipment, machinery, labor, and facilities. Users can schedule resources based on production requirements, track resource utilization, and identify opportunities for optimization. By maximizing resource efficiency, manufacturers can minimize idle time, reduce production costs, and improve overall productivity.ERPNext Manufacturing Services by Sigzen Technologies.
- Resource Allocation: Allocate manufacturing resources, including equipment, machinery, labor, and facilities, efficiently based on production requirements, capacity constraints, and resource availability, maximizing utilization and minimizing idle time.
- Capacity Planning: Plan and manage production capacity effectively by balancing workload, identifying bottlenecks, and optimizing resource utilization to meet production targets and customer demand without overloading resources.
- Resource Tracking: Track and monitor resource usage, downtime, and performance metrics in real-time to identify inefficiencies, optimize resource allocation, and improve overall operational efficiency.
10. Reporting and Analytics
Our solution offers comprehensive reporting and analytics capabilities to gain insights into production performance, resource utilization, cost trends, and other key metrics. Users can generate custom reports, dashboards, and KPIs to monitor performance, identify trends, and make data-driven decisions. Real-time visibility into manufacturing operations enables continuous improvement initiatives and enhances overall operational efficiency.ERPNext Manufacturing Services by Sigzen Technologies.
- Comprehensive Reporting: Generate comprehensive reports and analytics dashboards to monitor key performance indicators (KPIs), track production metrics, analyze trends, and identify areas for improvement across manufacturing operations.
- Customization Capabilities: Customize reports and analytics dashboards to suit specific business requirements, enabling stakeholders to access relevant insights and make data-driven decisions aligned with organizational goals.
- Drill-down Analysis: Perform drill-down analysis to explore detailed data underlying performance metrics, identify root causes of issues, and develop actionable insights to optimize processes, enhance efficiency, and drive continuous improvement.
11. Integration with External Systems
ERPNext Manufacturing Services seamlessly integrates with other business systems such as CRM, procurement, sales, and finance for end-to-end visibility and control over the manufacturing process. Data flows seamlessly between modules, eliminating manual data entry, reducing errors, and improving data accuracy. Integration with external systems enhances collaboration, streamlines business processes, and enables manufacturers to respond quickly to changing market conditions.ERPNext Manufacturing Services by Sigzen Technologies.
- Seamless Data Flow: Establish seamless integration with external systems such as CRM, procurement, sales, and finance to ensure consistent data flow and synchronization of information across the organization.
- Process Automation: Automate data exchange and business processes between ERPNext Manufacturing module and external systems to streamline operations, reduce manual effort, and eliminate data entry errors.
- Unified Information Hub: Create a unified information hub by integrating disparate systems, enabling stakeholders to access real-time data, streamline decision-making, and improve collaboration across departments and functions.
12. Work Order Management
Our Work Order Management module empowers manufacturers to efficiently plan, execute, and track production activities. Users can create work orders, allocate resources such as materials, machinery, and labor, and schedule tasks to meet production targets. Real-time tracking features enable supervisors to monitor progress, identify bottlenecks, and make necessary adjustments to ensure timely completion of orders.ERPNext Manufacturing Services by Sigzen Technologies.
- Seamless Tracking: Initiate, track, and manage manufacturing orders seamlessly from creation to completion, ensuring clarity and accountability throughout the production process.
- Resource Allocation: Allocate resources such as labor, equipment, and materials efficiently to fulfill work orders based on priority, capacity, and availability, maximizing productivity and minimizing delays.
- Real-time Visibility: Gain real-time visibility into work order status, progress, and completion times, enabling proactive decision-making and effective scheduling to meet production deadlines.
Conclusion
Your content highlights ERPNext Manufacturing Services by Sigzen Technologies, covering critical aspects like BOM Management, Work Order Management, Production Planning, MRP, Quality Control, Inventory Management, and more. It emphasizes streamlined processes, optimized resource utilization, and enhanced collaboration through seamless integration, offering manufacturers operational excellence and cost efficiency.