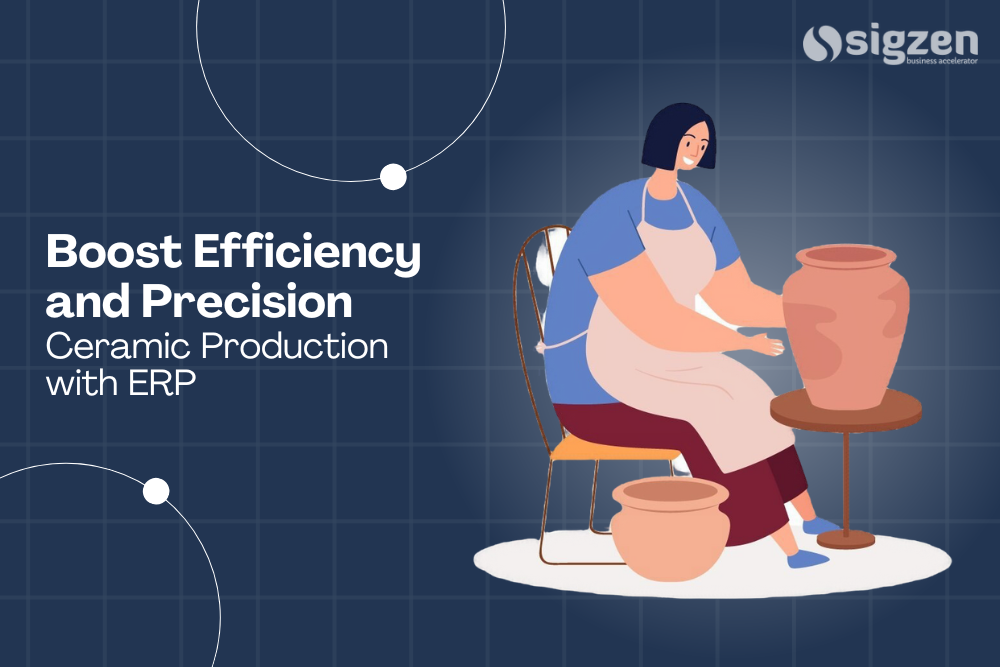
Manufacturing ceramic products involves intricate processes, from procuring raw materials to delivering finished goods. These operations demand precision, efficiency, and consistency to maintain product quality and reduce waste. However, managing such complexity with traditional methods can lead to inefficiencies, production delays, and unnecessary costs.
This is where ERP for Manufacturing emerges as a transformative solution. By automating and integrating core business processes, ERP systems revolutionize production management for manufacturing companies, ensuring streamlined operations, better decision-making, and enhanced profitability. Let’s explore how ERP systems, particularly ERPNext-based solutions like those offered by Sigzen, can optimize production for ceramic manufacturers.
Why Ceramic Manufacturers Need ERP Systems
Ceramic manufacturing involves multiple challenges, such as:
- Managing raw material procurement and inventory.
- Monitoring production workflows.
- Ensuring consistent product quality.
- Complying with industry regulations.
- Delivering orders on time.
Traditional systems often fail to address these challenges holistically, as they operate in silos, leading to data duplication and errors. On the other hand, ERP systems provide a centralized platform to integrate and automate all aspects of production management, making them indispensable for ceramic manufacturers.
Key Features of ERP for Manufacturing
- Centralized Data Management ERP systems unify data across departments, eliminating redundancies and ensuring real-time information access.
- Production Planning and Scheduling ERP systems like ERPNext’s Manufacturing Module optimize production schedules, allocate resources effectively, and minimize downtime.
- Inventory and Stock Management The Inventory Module tracks raw materials and finished goods in real-time, reducing stockouts and overstocking.
- Quality Control Ensuring consistent product quality is critical in ceramic manufacturing. ERPNext’s Quality Management Module automates quality checks and records deviations for corrective actions.
- Regulatory Compliance ERP systems simplify compliance by automating documentation and generating audit-ready reports.
- Cost Management By tracking production costs and material consumption, ERP systems help manufacturers identify cost-saving opportunities.
How ERP Optimizes Production Management for Ceramic Companies
1. Streamlining Raw Material Procurement
Efficient procurement is the backbone of ceramic production. ERP systems automate the purchase cycle, ensuring timely procurement of high-quality raw materials. ERPNext’s Purchase Cycle Module tracks supplier performance, streamlines order processing, and ensures cost efficiency.
2. Enhancing Production Planning
Ceramic manufacturing involves complex workflows, from molding and glazing to firing. ERP systems optimize these processes by:
- Generating accurate production schedules.
- Allocating resources efficiently.
- Monitoring progress in real time.
With Sigzen’s ERP solutions, ceramic companies can reduce bottlenecks and meet production deadlines seamlessly.
3. Improving Inventory Management
Maintaining the right inventory levels is crucial for uninterrupted production. ERP systems:
- Monitor stock levels in real time.
- Provide automated reordering alerts.
- Track material usage to prevent wastage.
The Inventory Module ensures that ceramic manufacturers always have the materials they need without overstocking, which ties up capital.
4. Automating Quality Control
Inconsistent product quality can tarnish a brand’s reputation. ERP systems automate quality control processes, from raw material testing to final product inspections. ERPNext’s Quality Control Features ensure that every ceramic product meets industry standards before leaving the factory.
5. Facilitating Regulatory Compliance
Ceramic manufacturers often face stringent regulatory requirements. ERP systems simplify compliance by:
- Maintaining accurate records.
- Automating document generation.
- Ensuring traceability across the supply chain.
This is especially beneficial during audits, as all necessary data is readily available.
Benefits of ERP Systems for Ceramic Manufacturers
1. Increased Efficiency
ERP systems automate repetitive tasks, reducing manual effort and errors. This allows manufacturers to focus on value-added activities, such as product innovation.
2. Enhanced Decision-Making
With real-time data and analytics, ERP systems empower managers to make informed decisions, whether it’s adjusting production schedules or optimizing resource allocation.
3. Cost Savings
By reducing material wastage, minimizing downtime, and improving inventory management, ERP systems lower operational costs.
4. Scalability
ERP systems are highly scalable, making them suitable for ceramic manufacturers of all sizes. As your business grows, the ERP system can adapt to handle increased production volumes and complexity.
5. Improved Customer Satisfaction
With streamlined operations and better product quality, ceramic manufacturers can meet customer demands more effectively, enhancing satisfaction and loyalty.
Real-World Example: Optimizing Ceramic Production with ERP
Case Study: A Ceramic Tile Manufacturer
Challenge: The company struggled with manual production scheduling, inconsistent product quality, and frequent stockouts, leading to delays and customer complaints.
Solution: The manufacturer implemented ERPNext, customized by Sigzen, to automate production management and quality control.
Results:
- Production efficiency increased by 25%.
- Quality control processes reduced defects by 15%.
- Inventory costs decreased by 20%.
Choosing the Right ERP for Ceramic Manufacturing
When selecting an ERP system, consider the following factors:
- Industry-Specific Features: Does the ERP system cater to the unique needs of ceramic manufacturing, such as batch tracking and quality control?
- Ease of Use: Is the system user-friendly for employees across departments?
- Integration Capabilities: Can the ERP system integrate with existing tools and systems?
- Customization and Scalability: Does the ERP system offer customization options and scalability for future growth?
- Support and Training: Does the provider offer ongoing support and training?
Sigzen’s ERP Solutions are tailored to meet the specific requirements of ceramic manufacturers, ensuring seamless implementation and maximum ROI.
Conclusion: Transform Your Ceramic Manufacturing with ERP
For ceramic manufacturers, staying competitive in today’s market requires more than traditional tools and methods. An ERP for Manufacturing offers a comprehensive solution to optimize production management for manufacturing, from raw material procurement to quality control.
By implementing a robust ERP system like ERPNext, customized by Sigzen, ceramic companies can streamline operations, reduce costs, and deliver superior products to their customers.
Ready to transform your ceramic manufacturing processes? Request a demo of Sigzen’s ERP solutions today and take the first step toward operational excellence.